Important user information
This manual explains how to install, operate and configure a MBDC-200. This device may only be used for the applications described in this document.
This manual is to be used with a MBDC-200 with firmware version 3.0.
These instructions are intended for use by trained specialists in electrical installation and control and automation engineering, who are familiar with the applicable national standards and safety procedures.
Safety Precautions
![]() |
ELECTRICAL HAZARD
Failure to follow these instructions could result in death or serious injury! |
Document conventions
Throughout this manual we use the following symbols and typefaces to make you aware of safety or other important considerations:
![]() |
Indicates a potentially hazardous situation that, if not avoided, could result in death or serious injury. |
![]() |
Indicates a potentially hazardous situation that, if not avoided, could result in damage to equipment. |
![]() |
Indicates information that is critical for successful application and understanding of the product. |
![]() |
Provides other helpful user information that does not fall in above categories. |
![]() |
Provides supplemental user information. |
Acronym
|
This typeface is used to introduce acronyms or product names. |
Command
|
This typeface is used to represent commands, prompts, input fields and filenames. In the context of programming it is used for functions, variable names, constants or class names. |
Placeholder
|
This typeface is used to represent replacable text. Replaceable text is a placeholder for data you have to provide, like filenames or command line arguments. |
User input
|
This typeface is used to represent data entered by the user or buttons. |
Screen output |
Screen output or program listing |
Introduction
The MBDC-200 is a Modbus/TCP data concentrator for Modbus RTU networks.
The data concentrator features an Ethernet port and two serial ports which can be configured as either RS-232 or RS-485 or combined to form one RS-422 port. It can be mounted on a DIN rail.
Usage and configuration of the data concentrator is simple and conveniently performed using a web browser which connects to the embedded web server.
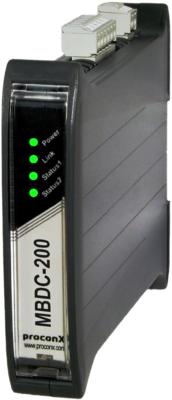
Possible areas of application are:
-
PLC connection
-
Operator panel interfacing
-
HMIs
-
SCADA integration
-
Remote control & monitoring
-
Data logging
Features
The MBDC-200 data concentrator provides the following key features:
-
Modbus/TCP protocol (Ethernet)
-
Modbus RTU protocol (either RS-232, RS-485 or RS-422, software configurable)
-
Embedded web server for easy configuration and commissioning using a web browser
-
Firmware upgradeable via Ethernet
-
DIN rail mountable
-
24 V DC (10-30 V) power supply
-
Status LEDs for power, Ethernet link, device status and communication status
Quick start checklist
-
Read this set of instructions properly and in its entirety.
-
Mount the unit.
-
Connect the power. Do not connect yet serial ports.
-
Configure the Ethernet communications settings with a web browser (using an Ethernet crossover cable) or with a terminal program like HyperTerminal (using a null modem cable)
-
Configure the serial line communication settings.
-
Configure the operational aspects of the device.
-
Wire serial line interfaces.
Description
The power and RS-485/RS-422 terminals are placed on the top side of the unit. The RS-232 and Ethernet connectors are placed on the bottom side of the unit as shown in the following illustration:
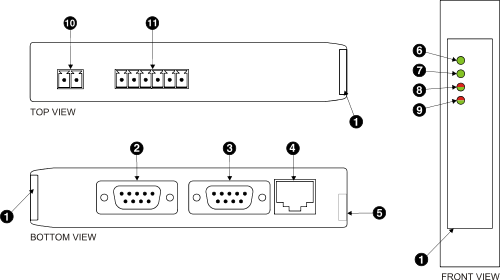











LED indicators
Four LEDs located at the front panel indicate the status of the device. The LEDs assist maintenance personnel in quickly identifying wiring or communication errors.
A LED test is exercised at power-up, cycling each LED off, green and then red for approximately 0.25 seconds. At the same time the power-on self test of the device is performed.
The following table outlines the indicator condition and the corresponding status after the power-on self test has been completed:
LED | Function | Condition | Indication |
---|---|---|---|
Power |
Power |
Off |
No power applied to the device. |
Green |
Power supply OK |
||
Link |
Ethernet link |
Off |
No Ethernet link |
Green |
Ethernet link OK |
||
Status1 |
Device status |
Off |
The device has an unrecoverable fault; may need replacing. |
Flashing green |
Device operational but needs commissioning due to configuration missing, incomplete or incorrect. |
||
Green |
The device is operating in normal condition. |
||
Flashing red |
Device operational but has a fault listed which requires acknowledgment. |
||
Red |
The device has an unrecoverable fault; may need replacing. Flashing sequence and rate of Status2 LED indicates fault class. |
||
Status2 |
Communication status |
Off |
No Modbus/TCP connection. |
Green |
Modbus/TCP connection established. |
||
Flashing red |
Communication error Modbus slave devices. |
Flashing red-green |
Installation
Regulatory notes
![]() |
|
This equipment has been tested and found to comply with the limits for a Class A digital device, pursuant to Part 15 of the FCC Rules. These limits are designed to provide reasonable protection against harmful interference when the equipment is operated in a commercial environment. This equipment generates, uses, and can radiate radio frequency energy and, if not installed and used in accordance with the instruction manual, may cause harmful interference to radio communications. Operation of this equipment in a residential area is likely to cause harmful interference in which case the user will be required to correct the interference at his own expense.
This Class A digital apparatus complies with Canadian ICES-003.
Unpacking, handling and storage
![]() |
|
Before connecting anything
![]() |
|
DIN rail mounting and removal
The MBDC-200 gateway is designed to be mounted on a 35 mm DIN rail according to DIN/EN 50022. The enclosure features a 35 mm profile at the back which snaps into the DIN rail. No tools are required for mounting. Please observe the rules outlined in [Mounting].
![]() |
To mount the unit on a DIN rail, slot the top part of the MBDC-200 into the upper guide of the rail and lower the enclosure until the bottom of the red hook clicks into place. |
![]() |
To remove the MBDC-200 from the DIN rail, use a screw driver as a lever by inserting it in the small slot of the red hook and push the red hook downwards. Then remove the unit from the rail by raising the bottom front edge of the enclosure. |
Mounting rules
The enclosure provides protection against solid objects according to IP 20 / NEMA Type 1 protection rating. When mounting the unit observe the following rules:
![]() |
|
Powering the MBDC-200
![]() |
Before connecting power please follow the rules in [Safety] and [Connecting]. |
Power is supplied via a 3.81 mm 2-pin pluggable terminal block located at the top side of the mounted unit (refer to [DescriptionDiagram]). The following table and picture shows the power terminal socket pinout:
![]() |
|
![]() |
Make sure that the polarity of the supply voltage is correct before connecting any device to the serial ports! A wrong polarity can cause high currents on the ground plane between the V- power supply pin and the serial port ground pins, which can cause damage to the device. |
Wiring the RS-485/422 interface
The RS-485/422 port is used for integrating the MBDC-200 into a two-wire or four-wire Modbus over Serial Line network. The use of either the RS-485 or RS-422 interface must be configured using the web interface (See [ModbusConfig]). The MBDC-200 is a Modbus Master device on this interface.
The RS-485 and RS-422 signals are located at the 3.81 mm 6-pin pluggable terminal block on the top side of the mounted unit (refer to [DescriptionDiagram]). The following table and picture shows the pinout:
![]() RS-485 ![]() RS-422 |
|
-
Line termination is required and is typically done with a 120 Ohm 1/4 W resistor. For RS-485 operation the bus must be terminated at both ends. For RS-422 operation a termination resistor must be inserted between the RX+/RX- signals.
-
Maximum number of RS-485 nodes without repeater is 32.
-
Stub connections off the main line should be avoided if possible or at least be kept as short as possible. Stub connections must not have terminating resistors.
-
Maximum cable length to 1200 m (4000 ft).
-
To assure a high degree of electromagnetic compatibility and surge protection the cable should be twisted pairs and shielded. An additional cable conductor or pair may be used for the GND reference.
![]() |
Do not connect the cable shield to the GND pins! Use an external chassis ground connection to terminate the shield. |
Wiring the RS-232 interface
The RS-232 port can alternativly be used for serial communication to a Modbus Slave device instead of RS-485. The use of the RS-232 interface must be configured using the web interface (See [ModbusConfig]). The MBDC-200 is a Modbus Master device on this interface.
The Modbus RS-232 connector is a male 9-pin D-sub type located at the bottom side of the mounted unit (refer to [DescriptionDiagram]). It has industry standard EIA-574 data terminal equipment (DTE) pinout as shown in the following table and picture:
![]() |
|
-
Maximum cable length is 15 m (50 ft) or a length equal to a line capacitance of 2500 pF, both at the maximum standard bit rate of 20 kbps. If operating at higher bit rates the maximum cable length drops to 3 m (10 ft) at a bit rate of 57.6 kbps.
-
To assure a high degree of electromagnetic compatibility and surge protection the RS-232 cable should shielded. The shield shall be connected to an external chassis ground at the either or both ends, depending on the application.
-
The shield must not be connected to the GND pin.
![]() |
To connect the MBDC-200 to a PC (Personal Computer) or any other device with data terminal equipment (DTE) pinout you need a null-modem or cross-over cable. |
Connecting Ethernet
The following table describes the 10BASE-T Ethernet RJ-45 connector pinout:
![]() |
|
-
We recommend to use Category 5 UTP network cable.
-
Maximum cable length is 100 m (3000 ft).
Ethernet & IP configuration
Before configuring the MBDC-200, obtain a unique static IP address, subnet mask, and default gateway address from your network administrator.
The factory default IP address of the MBDC-200 is 169.254.0.10 which is in the Automatic Private IP Addressing (APIPA) address range.
There are several methods of configuring the unit’s IP address:
-
Removing your PC from your corporate network and using a cross-over network cable (see [ConfigCrossOver]).
-
Via the Serial Port 1 and a terminal program like HyperTerminal (see [ConfigTerminal]).
-
Leaving your PC connected to your corporate network and temporarily changing the IP settings on your PC to match the subnet of the MBDC-200 (see [ConfigChangeIP]).
![]() |
In order to connect to the MBDC-200 via TCP/IP, your PC must be on same IP subnet as the gateway. In most situations this means that the first three numbers of the IP address have to be identical. |
IP setup using a web browser and a cross-over network cable
This method applies only to operating systems like Windows, which support APIPA (Automatic Private IP Addressing). It also requires your PC to be configured for DHCP. If your computer is configured with a static IP address, follow the procedure in [ConfigChangeIP].
-
Disconnect your PC from your corporate network. If your computer is configured for DHCP it should now automatically fall back to use a default IP address from the APIPA range 169.254.x.x (Windows PCs only).
-
Connect an Ethernet crossover cable from the MBDC-200 to the computer.
-
Start Internet Explorer.
-
In the address box, type 169.254.0.10 and then press Enter.
-
Click Configuration… and then Ethernet & IP in the menu on the left side of the page.
-
Enter the IP address, subnet mask, and gateway address assigned to your MBDC-200, then click Save.
-
Reconnect your computer to your corporate network.
IP setup using a terminal program like HyperTerminal
-
Connect a null modem RS-232 cable between your PC and the MBDC-200’s Serial Port 1.
-
In Windows XP, click Start, point to All Programs, point to Accessories, point to Communications, and then click HyperTerminal.
-
When HyperTerminal starts, it opens a dialog box and asks for a name for the new connection. Enter a name (for example, deviceconfig) then click OK.
-
The Connect to dialog opens. Select the COM port you will be using in the Connect using drop-down list box, then click OK.
-
Select 9600, 8, None, 1, None in the COM Properties dialog, then click OK.
-
HyperTerminal is now connected to the serial line.
-
Keep the space bar pressed in HyperTerminal and power-cycle your device at the same time.
-
A menu should appear after one or two seconds showing device information, the current IP configuration and a > prompt.
-
Type SETIP, then press Enter within 10 seconds after the prompt is shown:
-
The device will show current values and prompt for new values for IP address, net mask and gateway address. Enter the new values and press Enter. A key press must be received at least every 10 seconds otherwise the device will go back to RUN MODE and resume normal operation.
-
The gateway will return to the main prompt. Type X and press Enter to leave DIAG MODE and resume normal operation indicated with RUN MODE.
Temporarily changing the IP settings on your PC
This method involves manually assigning an IP address to your PC in the same subnet as the gateway. The default subnet of the gateway is 169.254.0.0/16.
-
Connect the MBDC-200 to your Ethernet network.
-
On a Windows PC, open the Control Panel and double-click on Network Connections. Right-click on the Network Connection associated with your network adapter and select Properties:
This will show the Local Area Connection Properties Dialog:
-
Select the Internet Protocol (TCP/IP) entry and click on Properties to open the TCP/IP Properties dialog as shown below:
-
Write down your current settings so they can be restored later.
-
Select Use the following IP address and configure a static IP address in the same subnet as the device, for example 169.254.0.1 and the subnet mask 255.255.0.0. Click OK to save the changes.
-
Start Internet Explorer.
-
In the address box, type 169.254.0.10 and then press Enter.
-
Click Configuration… and then Ethernet & IP in the menu on the left side of the page.
-
Enter the IP address, subnet mask, and gateway address assigned to your MBDC-200, then click Save.
-
Restore your computer’s original settings.
Web browser based management
The MBDC-200 incorporates an embedded web server. This allows you to connect to the device and monitor and configure it using a web browser. Most browsers should work, provided they support JavaScript. We recommend Internet Explorer 6.0 or higher.
Connecting to the MBDC-200
Once you made sure that your PC is configured to be on the same subnet as the MBDC-200, start your web browser. In the address box, type the IP address of your device (169.254.0.10 is the default), and then press Enter. (See [EthernetConfig])
The web browser will establish communication with the embedded web server and an overview page similar to the following picture will appear:
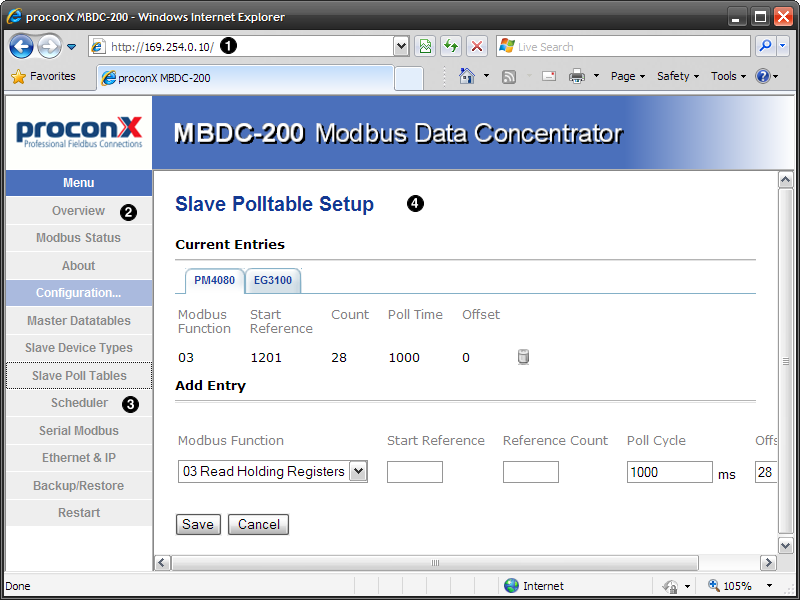




Use the menu bar shown on the left side to navigate the different pages.
![]() |
In order to connect to the MBDC-200 via TCP/IP, your PC must be on same IP subnet as the data concentrator. In most situations this means that the first three numbers of the IP address have to be identical. |
Monitoring and diagnostic
The MBDC-200 offers several web pages which allow monitoring of the status of the different communication networks and the device performance.
Device status
The Overview page shows the principal device status as shown in the following picture:
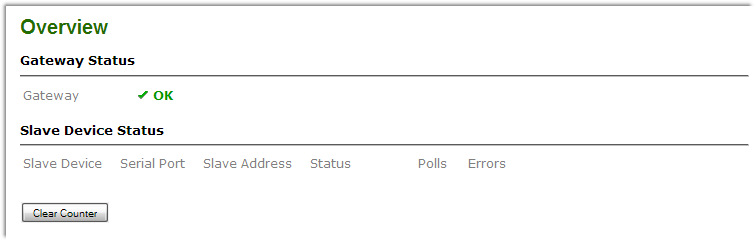
The value shown in the Device row represents the device status register which keeps track of run-time faults. All run-time faults are latched and must be reset by the user. The following faults can be listed here:
- OK
-
The device is fault free.
- Watchdog reset
-
This warning indicates that the device was reset by it’s internal watchdog supervision circuit.
- Brown out reset
-
This warning indicates that the device was reset by it’s internal supply voltage monitoring circuit. This fault occurs when the supply voltage drops below the lower limit.
- Device out of memory
-
This warning indicates that the internal dynamic memory has been exhausted and due to this a certain function could not be completed.
- Device configuration data write failure
-
This alarm indicates that the configuration data could not be written to the non-volatile memory. Configuration data changes will be lost once the device is power-cycled or reset.
- Reset to factory defaults
-
This alarm indicates that the device' configuration data was reset to factory defaults. The device requires re-commissioning.
Modbus connection status
The Modbus Status page shows status and statistics about the Modbus traffic. These values provide valuable information used to troubleshoot Modbus network problems. This page is automatically updated every 5 seconds.
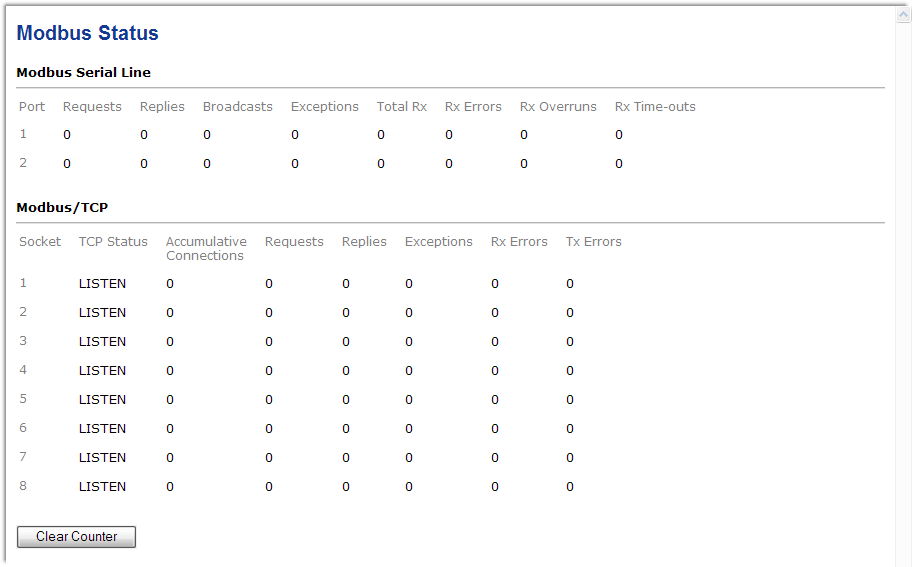
![]() |
This page shows accumulated readings since the MBDC-200 was last activated or reset. If power to the MBDC-200 is lost, all cumulative values are reset to zero. |
The following statistics are maintained:
- TCP status
-
Status of the TCP/IP connection as per TCP finite state machine (refer to RFC 793). If no client is connected the status indicates LISTEN. If a client is connected, it’s IP address is shown.
- Accumulative connections
-
A counter that increments each time a client opens a Modbus/TCP connection.
- Requests
-
A counter that increments each time an inbound request message is successfully received.
- Replies
-
A counter that is incremented each time a reply message is sent back to the master. This includes exception replies.
- CRC errors
-
A counter that increments each time a message is received that has a CRC that does not match what is calculated. Typically the result of wiring issues. Messages with CRC errors are discarded and not replied to.
- Invalid frames
-
A counter that increments each time a malformed Modbus frame is detected. Malformed frames are for example messages larger than the allowed maximum PDU size defined in the Modbus standards. This can be caused by non-Modbus traffic on the network.
- Rx time-outs (Modbus serial line)
-
A counter that increments each time an inter-character time-out occurred during the reception of an inbound message.
- Rx time-outs (Modbus/TCP)
-
A counter that increments if the master connection has timed out. Subsequently the connection is terminated by the MBDC-200. A time-out occurs if no Modbus request is received from a connected client within a 10 second period.
- Tx time-outs
-
Number time-outs occurred when attempting to send a reply message.
The cumulative diagnostic data is reset when the device is power cycled or reset. The data is also reset by pressing the Clear Counter button.
Finding the firmware version and serial number
Click on the About menu entry on the menu bar to show the product information as shown below:
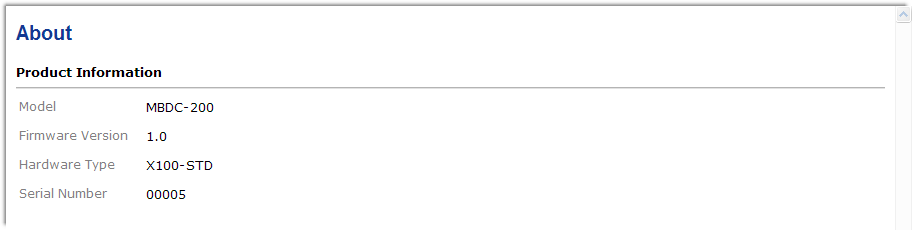
This product information is important for service and support inquiries. The following product information is provided:
- Product name
-
The name of the product.
- Hardware version
-
MBDC-200 hardware version.
- Firmware version
-
The firmware version that is installed on the MBDC-200.
- Serial number
-
The serial number of the MBDC-200. The serial number is specific to your device.
Configuring and commissioning
The configuration pages are accessed by clicking on the Configuration… menu entry on the menu bar which then expands a configuration sub-menu. All configuration settings are kept in the device' non-volatile memory.
![]() |
If you make changes to any settings, remember to save each page before changing to a different page! |
Configuring Ethernet and IP
Select the Configuration→Ethernet & IP sub-menu from the menu bar to open the Ethernet and IP settings which are shown below:
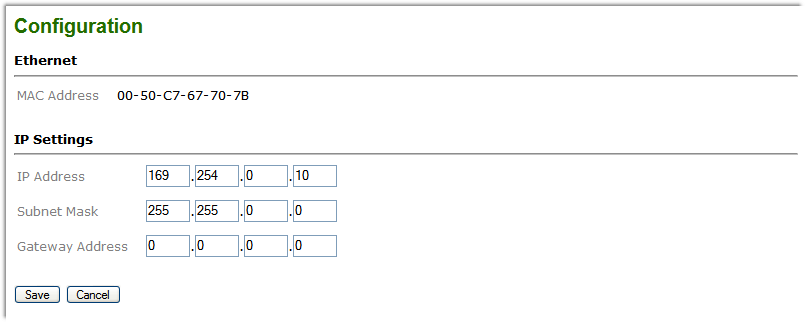
The following Ethernet parameters are shown:
- MAC address
-
The device' unique MAC address. This number is hard coded and cannot be changed.
The following Internet protocol (IP) settings can be entered:
- IP address
-
The IP address assigned to this device.
- Subnet mask (also known as indexterm2:[network mask])
-
If you have a router, enter the subnet mask for the segment to which this device is attached.
- Gateway address
-
If your network segment has a router, enter its IP address here. Otherwise leave the address as 0.0.0.0.
Once you click Save the new settings are stored and applied instantly. The new settings are confirmed with the following page:

![]() |
Please write down the new IP address so you are able to communicate with the device in the future! |
Configuring serial line Modbus
The Modbus settings for serial line can be configured to match the network configuration of your Modbus master device. Select the Configuration→Modbus sub-menu from the menu bar to open the Modbus settings which are shown below:
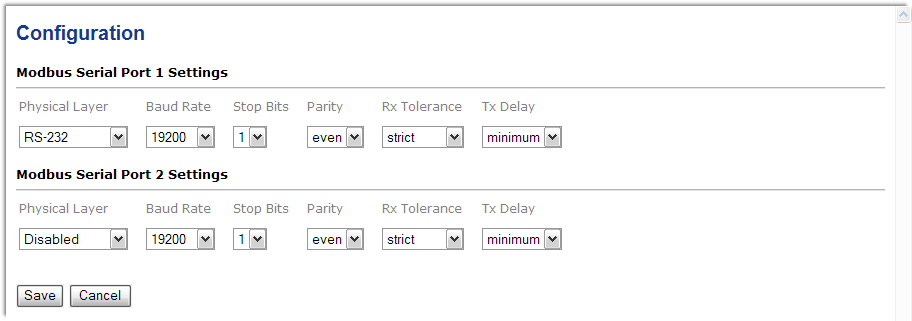
The following Modbus settings can be entered:
- Physical layer
-
Can be set to two-wire RS-485, RS-422 or RS-232 mode. RS-485 is the default. Depending on this setting either the D-sub (RS-232) connector or the terminal block connector (RS-485/422) of the MBDC-200 is utilized.
- Transmission mode
-
Only RTU mode can be selected here.
- Baud rate
-
9600 and 19200 are the most common baud rates for Modbus. 19200 is the default setting.
- Data bits
-
Only 8 data bits can be selected here which is a requirement for RTU.
- Stop bits
-
Can be configured to be 1 or 2. The Modbus standard mandates that 2 stop bits are configured when using no parity.
- Parity
-
Changes parity mode to either none, even or odd. The default parity mode for Modbus is even parity.
Once you click Save the new settings are stored and applied instantly. A confirmation message is shown.
Remote restarting the device
You can perform a remote restart of the device from the web interface. A remote restart is similar to power cycling the device. Possibly connected clients are disconnected and communication is interrupted until the device has rebooted.
To perform a remote restart, click on the Configuration sub-menu and then click on the Restart menu entry. This will open the device restart page as shown below:

Click on the Restart button to perform a restart of the device. The restart is confirmed with the following notification:

Please allow a few seconds before continuing working with the device as it has to fully start-up first, before being able to respond to further web browser requests.
![]() |
After a remote restart a Watchdog reset alarm is shown on the device' home page. This is a side-effect of the remote restart procedure and the alarm shall be ignored and cleared. |
Programming the communciation flow
Compared to an ordinary Modbus gateway, the configuration of a Modbus data concentrator requires additional configuration steps. The data concentrator requires knowledge of the type of slave devices connected and also how the data in those slave devices is structured as well as what data items the master devices are interested in.
The following configuration steps must be performed:
-
Nominate the different types of the slave devices to be connected.
-
Configure how the data of interest in those slave devices is structured.
-
Define the size and location of the data area the master devices will see.
-
Define how the data of an individual slave device is mapped into that master data area.
Slave Device Types Setup
One of the first steps to configure the data concentrator is to identify the slave devices by a name.
Click on Configuration→Slave Device Types. In the Add Entry section enter a name for the slave device and click the Save button.
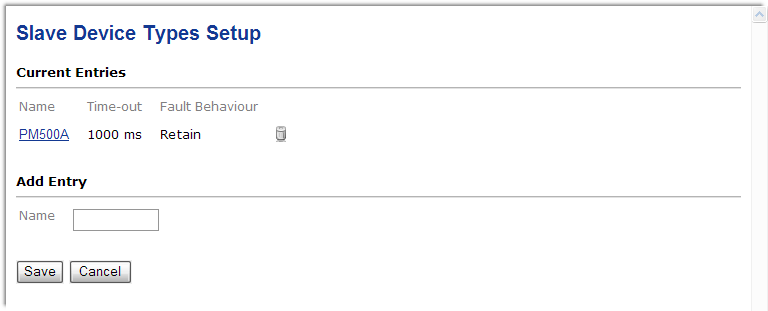
- Name
-
Textual identifier for a class of devices sharing the same Modbus register layout.
- Fault Behaviour
-
Defines how a communciation error should be treated.
Slave Polltable Setup
Once the Slave Device Types are defined by name (refer to [SlaveDeviceTypesSetup]), a set of registers can be associated with each device type. This set of registers is called a Polltable.
Click on Configuration→Slave Polltable Setup.
This page shows which Modbus register ranges shall be polled for a particular device type. You can select a device on the device tab and add new entries and remove existing entries.
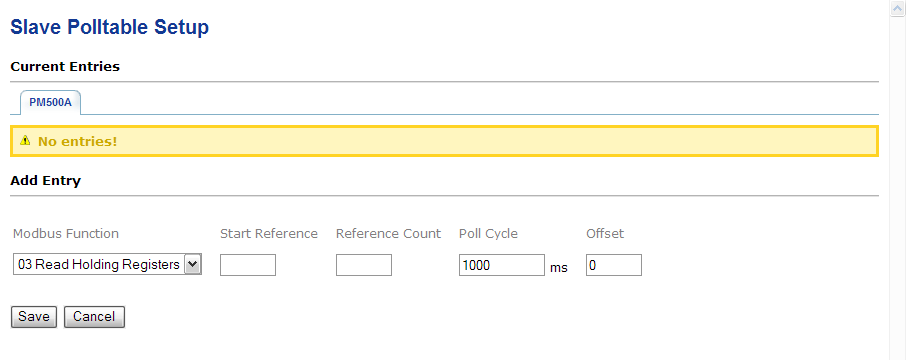
- Modbus Function
-
The Modbus function code to be used for the Modbus transaction.
- Start Reference
-
Defines the start register for the Modbus transaction. This number is 1-based meaning the first Modbus register is identified as register 1.
- Reference Count
-
Defines how many registers are to be read or written.
- Poll Cycle
-
Defines the minimum time span between two consecutive Modbus transactions of this type. Please note, that this is a minimum time and the actual cycle time may be longer depending on the scheduling order of other Modbus transactions.
- Offset
-
The offset defines where in relation to the start of this poll table the returned data is to be stored. In most situations the offset is 0 for the first entry and then incremented by the number of registers polled by the previous entry.
Example
In this example we are using the Schneider PM500 power meter with the following Modbus table layout:
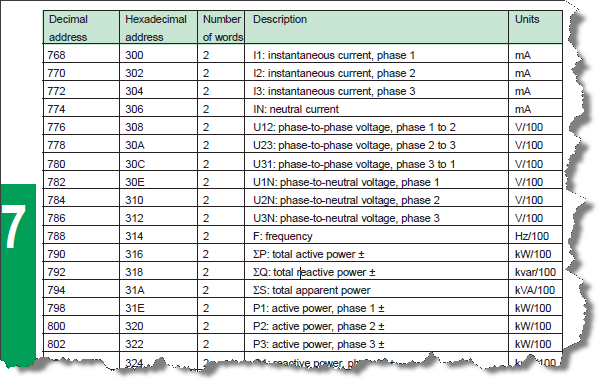
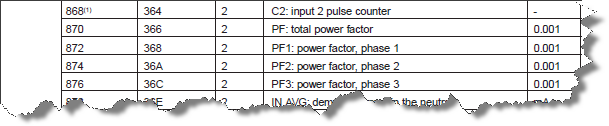
We are interested in the current, voltage and power values which we read in one block starting at register 768 with a count of 37 registers. In addition we like to read the energy counters which we read using a second Modbus transaction from start address 870 and a count of 8 registers. Because the PM500 document is using 0-based register numbering, we have to add an offset of 1 to all register addresses before they are entered into the MBDC-200.
This results in the following configuration Slave Polltable:
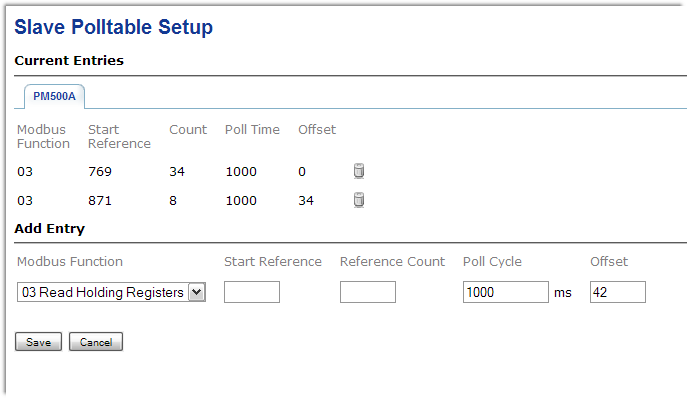
Master Datatable Setup
The Master Datatable defines how big the data area is a master can access as well as its start address and a slave ID.
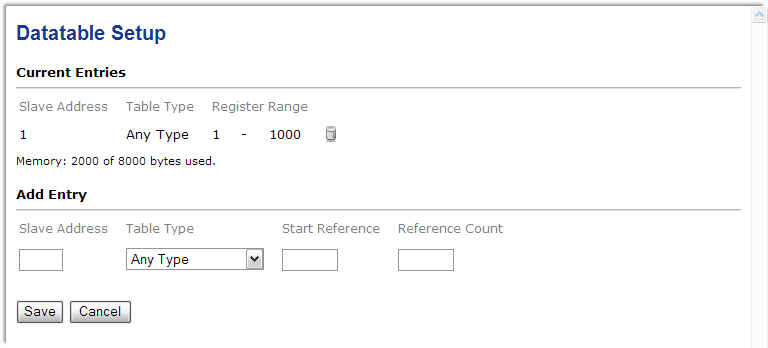
- Slave Address
-
This is the slave ID or unit ID this data table must be addressed with.
- Table Type
-
This defines what Modbus data types this table can hold. It also limits the Modbus function codes a Master can use to access the data table.
- Start Reference
-
This value defines the first register of the table. This number is 1-based meaning the first Modbus register is identified as register 1.
- Reference Count
-
The number of registers this table can hold.
Scheduler Configuration
Entering scheduler entries is the last step of the data concentrator’s configuration. Once a scheduler entry has been made, the MBDC-200 starts communicating with the relevant slave device.
To add or delete a scheduler entry, select the Configuration→Scheduler Configuration sub-menu from the menu bar.
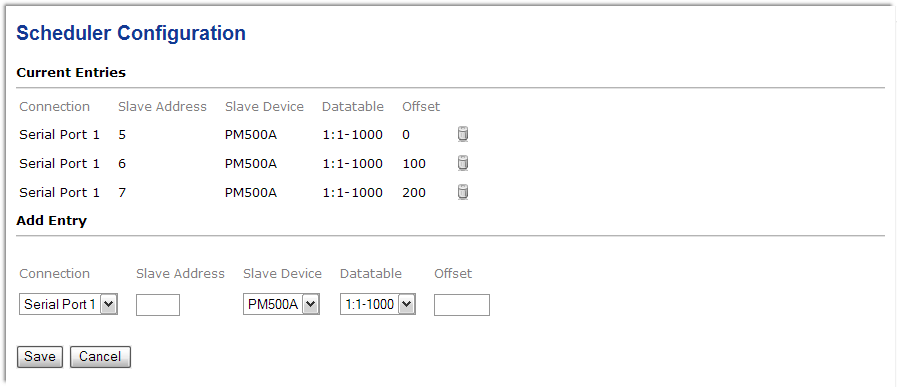
- Connection
-
The serial port where the slave device is physically connected to.
- Slave Address
-
The Modbus Slave ID of the slave device.
- Slave Device
-
The type of the slave device (refer to [SlaveDeviceTypesSetup]). This selection defines which register layout is used.
- Datatable
-
The Master Data Table (refer to [MasterDatatableSetup]). The Master Data Table is the location where read data is stored and data to be written to the slave device is taken from.
- Offset
-
A register offset where the data is located within the Master Data Table.
The order and timing of the Modbus communication cycles depends on the poll cycle, the order of poll table entries and the order of the scheduler entries.
Decommissioning
Before disconnecting the MBDC-200 unit please follow the rules in [Safety].
Disconnecting
![]() |
|
Disposal
![]() |
This product must be disposed of at a specialized electronic waste recycling facility. Do not dispose of in domestic waste. |
Appendix A: Specifications
Product name
|
MBDC-200 |
Interfaces |
|
Ethernet |
1 |
Serial ports |
2, software configurable as either 2 x RS-232 or 2 x RS-485 or 1 x RS-232 + 1 x RS-485 or 1 x RS-422 |
User interface |
|
LED indicators |
Power (green), Ethernet link (green), 2 status (bi-color red/green) |
Monitoring & configuration |
Web browser based |
Diagnostic |
|
High availability features |
Watchdog supervision, brown-out detection |
Serial Port 1 RS-232 interface |
|
Connector |
male 9-pin D-sub, DTE, EIA-574 pin-out |
Physical layer |
EIA-232-F |
Isolation |
non-isolated |
Signals |
RXD, TXD, RTS, CTS, DTR, DSR, DCD, RI |
Speed |
300, 600, 1200, 2400, 4800, 9600, 19200, 57600, 115200 bps |
Protocols |
Modbus RTU master |
Serial Port 1 RS-485/RS-422 interface |
|
Connector |
3.81 mm 6-pin pluggable terminal block header |
Physical layer |
EIA-485-A, 2-wire or 4-wire |
Isolation |
non-isolated |
Speed |
300, 600, 1200, 2400, 4800, 9600, 19200, 57600, 115200 bps |
Max. number of nodes |
32 |
Protocols |
Modbus RTU master |
Serial Port 2 RS-232 interface |
|
Connector |
male 9-pin D-sub, DTE, EIA-574 pin-out |
Physical layer |
EIA-232-F |
Isolation |
non-isolated |
Signals |
RXD, TXD |
Speed |
9600 bps |
Protocols |
Modbus RTU master |
Serial Port 2 RS-485 interface |
|
Connector |
3.81 mm 6-pin pluggable terminal block header |
Physical layer |
EIA-485-A, 2-wire |
Isolation |
non-isolated |
Speed |
300, 600, 1200, 2400, 4800, 9600, 19200, 57600, 115200 bps |
Max. number of nodes |
32 |
Protocols |
Modbus RTU master |
Ethernet port |
|
Connector |
8-pin RJ-45 socket for Cat 5 UTP |
Physical & Data Link Layer Layer |
IEEE 802.3i 10BASE-T |
Isolation |
1.5 kV galvanic |
Speed |
10 Mbit/s |
Max. cable length |
100 m (328 ft) |
Ethernet frame types |
802.3 |
Protocols |
Modbus/TCP slave, HTTP, IP, TCP, ARP |
Concurrent connections |
8 Modbus/TCP slave, 2 HTTP |
Power supply |
|
Connector |
3.81 mm 2-pin pluggable terminal block header |
Voltage |
10-30 V DC |
Current |
30 mA typical @ 24 V DC |
Intrinsic consumption |
750 mW |
Electromagnetic compatibility |
|
Emissions (radiated and conducted) |
AS/NZS CISPR 22 / EN 55022 (Class A) |
Immunity |
EN 55024 |
Electrostatic discharge |
EN 61000-4-2 |
Radiated RF |
EN 61000-4-3 |
Fast transients |
EN 61000-4-4 |
Conducted RF |
EN 61000-4-6 |
Enclosure |
|
Material |
Self-extinguishing PC/ABS blend (UL 94-V0) |
Mounting |
35 mm DIN rail (EN 60715) |
Classification / Type rating |
IP 20 / NEMA Type 1 |
Cooling |
Convection |
Environmental |
|
Operating temperature |
0 to 60 °C / 32 to 140 °F |
Storage temperature |
-25 to 85 °C / -13 to 185 °F |
Humidity rating |
10 to 95% relative humidity, non condensing |
Operating ambience |
Free from corrosive gas, minimal dust |
Physical |
|
Dimensions |
101 x 22.5 x 120 mm / 3.98 x 0.886 x 4.72 in |
Weight |
0.12 kg / 0.265 lb |
Compliance |
|
Australia |
C-Tick |
Europe |
CE, RoHS |
USA |
FCC Part 15 (Class A) |
Canada |
ICES-003 (Class A) |
Dimensions
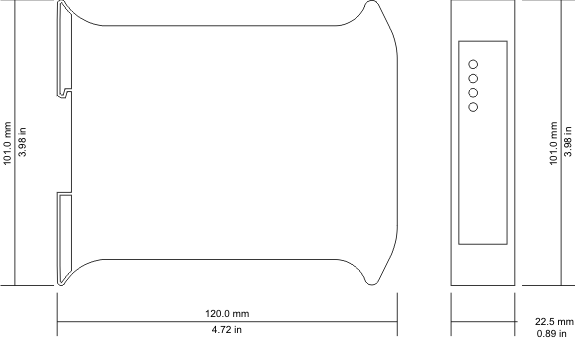
Glossary
- 10BASE-T
-
10 Mbit/s twisted pair Ethernet standard. Standardized in IEEE 802.3i
- APIPA
-
Automatic Private IP Addressing
-
-
- Class A
-
Class A equipment is that used in commercial or light industrial environments.
- DCE
-
Data communications equipment. DTE and DCE devices have different pinouts for RS-232 connectors. A Modem for example is a DCE.
- DIN rail
-
35 mm wide mounting bracket standardized in DIN/EN 50022.
- DTE
-
Data terminal equipment. DTE and DCE devices have different pinouts for RS-232 connectors. A PC for example is a DTE.
- EIA-232
-
Standard for serial transmission of data between two devices, also known as RS-232 and V.24.
- EIA-422
-
ANSI/TIA/EIA-422 standard for serial transmission of data between two devices, also known as RS-422 and V.11.
- EIA-485
-
ANSI/TIA/EIA-485 standard for serial transmission of data between multiple devices, also known as RS-485.
- EIA-574
-
Standard for the pinout of serial D-sub connectors.
- EMC
-
Electromagnetic compatibility
- EMI
-
Electromagnetic interference
- ESD
-
Electrostatic discharge. ESD can damage electronic equipment.
- Ethernet
-
The standard for local area networks developed jointly by Digital Equipment Corp., Xerox, and Intel. Ethernet is used as the underlying transport vehicle by several upper-level protocols, including TCP/IP.
- IEEE
-
Institute of Electrical and Electronics Engineers
- IP
-
Ingress Protection Rating standardized in IEC 60529. Standard for various grades of electrical enclosures.
- IP address
-
A numeric address used by computer hosts to transmit and receive information over the Internet.
- ISO
-
International Standards Organisation
- Gateway
-
A network device that passes data between different networks or fieldbusses.
- Gateway address
-
The IP address of the gateway or router used to access the Internet from the local are network.
- MAC address
-
Every piece of Ethernet hardware has a unique number assigned to it called it’s MAC address. MAC addresses are administered and assigned by the IEEE organization.
- Modbus
-
Fieldbus protocol used in the process automation industry. It uses a master and slave structure. Originally developed by Modicon, now part of Schneider Automation.
- NEMA
-
National Electrical Manufacturers Association. NEMA defines standards for various grades of electrical enclosures.
- Node
-
A communications device on the network.
- PC/ABS
-
Polycarbonate-ABS. Widely used thermoplastic material.
- PLC
-
Programmable Logic Controller
- RS-232
-
See EIA-232.
- RS-422
-
See EIA-422.
- RS-485
-
See EIA-485.
- Subnet mask
-
A numeric address used in conjunction with an IP address to segment network traffic; used to restrict transmissions to certain subnets.
- Switch
-
A device that facilitates transmissions between nodes in a star-formed network.
- TCP/IP
-
Transport Control Protocol/Internet Protocol. Connection-orientated transfer protocol.
- Telnet
-
A network protocol (RFC 854) for character based terminal access to remote machines.
- UL 94
-
Plastics flammability standard released by Underwriters Laboratories of the USA.
Document revision history
2011-04-06
|
Initial Release |
2012-11-02
|
Updated for firmware release 3.0 |
No part of this material may be reproduced or transmitted in any form or by any means or used to make any derivative work without express written consent from the copyright holders.
proconX is a trademark of proconX Pty Ltd. Modbus is a registered trademark of Schneider Automation Inc. All other product and brand names mentioned in this document may be trademarks or registered trademarks of their respective owners.
proconX Pty Ltd makes no warranty for the use of its products, other than those expressly contained in the Company’s standard warranty which is detailed in the Terms and Conditions located on the Company’s Website. The Company assumes no responsibility for any errors which may appear in this document, reserves the right to change devices or specifications detailed herein at any time without notice, and does not make any commitment to update the information contained herein. No licenses to patents or other intellectual property of proconX are granted by the Company in connection with the sale of proconX products, expressly or by implication. proconX products are not authorized for use as critical components in life support devices or systems.
We provide an electronic support and feedback system for our proconX products. It can be accessed through the following web link:
Your feedback and comments are always welcome. It helps improving this product.
For further information about the MBDC-200 product or this document please contact us at:
proconX Pty Ltd Unit 7 / 14 Argon St Sumner QLD 4074 Australia Tel +61-7-3376 3911 Website: http://www.proconx.com/mbdc200